|
 |
 |
KingKL Castingmould appoints a project manager to each
individual project and client. All project manager are qualified engineers.
TOOLING PROCESS TRACKING
To efficiently manage projects and achieve the required lead time,Microsoft
Project is used to monitor the progress of manufacture.Progress charts
are issued every week via email including digital photographs of the
work in progress, creating a “real-time”
tooling progress assessment available to our clients.
ON-LINE COMMUNICATION
KingKL Castingmould uses an integrated approach to establish the best
process for the manufacturing of your product.Once the production
plan is in place, we work with our clients in “real-time”,utilize
web-based communication, design and file transfer tools that streamline
every step of processing and fulfilling the project.
FILE TRANSFER
Files can be imported and exported in all common formats,including
· IGES (Initial Graphics Exchange
Specification)
· DXF (Drawing Interchange Format)
· STEP
· Native Parasolids
· Autocad DWG files
· Unigraphics PRT files
If you file are in another format, contact your project manager and
we arrange to accommodate your needs. File transfers are done via
Internet FTP or email. To quickly and easily transfer a design file
to KingKL Die Casting, contact your project
manager for instructions.
As one of clients your main
benefits are |
·
Direct Manufacturer |
·
One-stop Manufacturing Solutions |
·
Extensive Variety of Manufacturing Capabilities |
·
Low Engineering and Tooling Cost |
·
Low Per-part Pricing |
·
Fast Time to Market |
·
Consistent High Quality and Reliability |
·
Field Proven Application Solutions |
·
Engineering Support Services |
·
Legal Responsibility and Accountability |
·
Unique Bridge for International Gap |
·
Flexibility for the Customer |
|
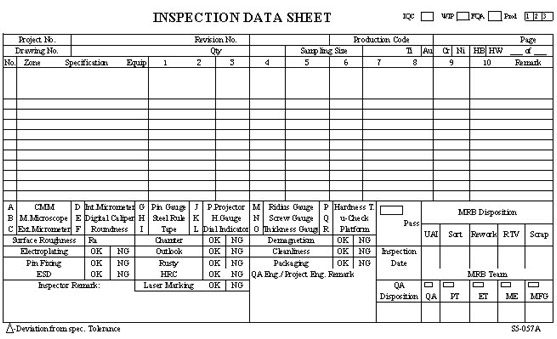 |
Project procedure: |
|
|